HG120-3AB PVC & Polylaminate Wine Capsule Machine
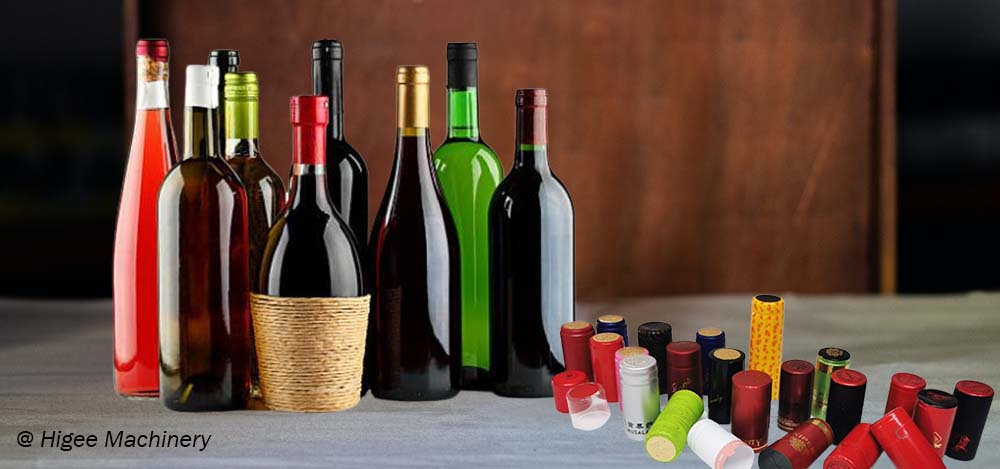
Fully Automatic PVC & Polylaminate Multifunctional Wine Capsule Making Machine
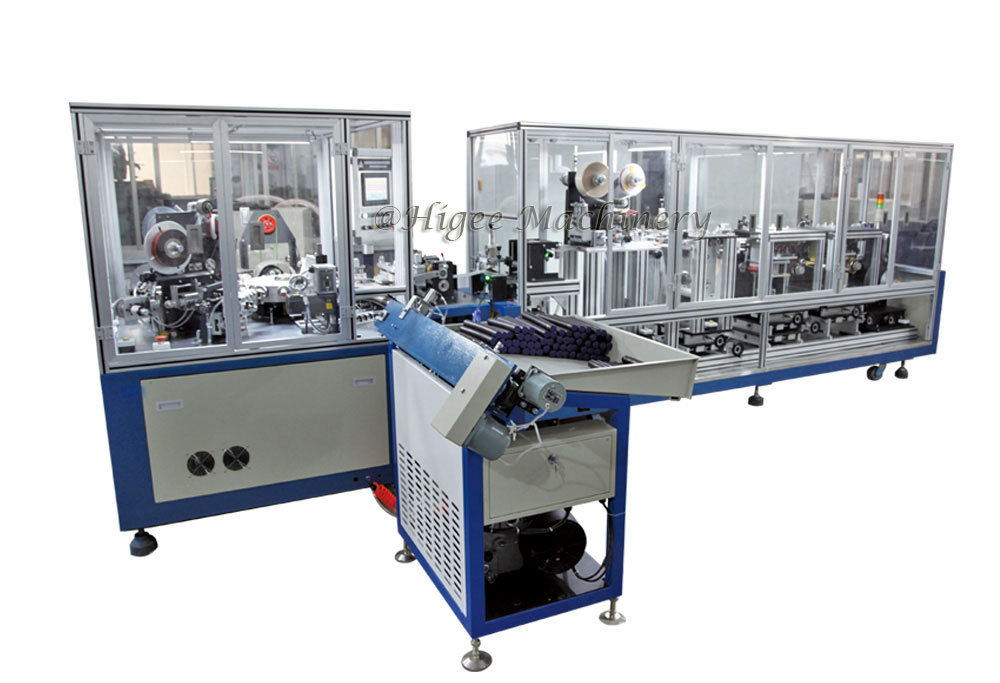
Application
This wine capsule making machine using Polylaminate (Aluminum plastic compound material) shrinkable film to make heat shrink capsules in different sizes and thickness with customized decoration. It is with good accuracy and good performance.
Option Functions
* Top Disc 1 Color /2 Colors Hot Stamping
* Top Disc 1 Color Relief Printing
* Top Disc Embossing and Breath Hole
* Skirt 1 Color/ 2 Colors Hot Stamping
* Skirt Tear tab each opening
* Skirt Horizontal Perforation
* Skirt Vertical Perforation
* Skirt C Type Punch Opening
Technical Parameters
No. |
Items |
Parameters |
1 |
Model |
HG120-3AB |
2 |
Material |
PVC/Polylam film |
3 |
Design production capacity |
130pcs/minute |
4 |
Top diameter of capsule |
30mm~37mm |
5 |
Bottom diameter of capsule |
Maximum 38mm |
6 |
Height of wine capsule |
45mm ~75mm |
7 |
Taper |
about 1.5°~3° |
8 |
Thickness of material |
0.065 mm ~0.08mm |
9 |
Machine power |
14.5kw |
10 |
Power supply |
3 Phase 380V 50HZ (if different should be informed) |
11 |
Weight of machine |
Abt. 4600kg |
12 |
Size (L*W*H) |
Abt. 6000mmx3000mmx1700mm |
Features
1.Rear rack working process
Automatic capsule material releasing system
Releasing automatically according to the next main material needed.
The tensile force adjusting system
It is used to adjust the pulling tightness of the main material to ensure that the material move straightly.
First-level photoelectric Deviation rectification system
This can make sure the material roll go in a straight line along the specified position during unwinding in case the material roller edge is not regularly in a line.
4) Skirt hot stamping system
It can do a hot stamping of a fine pattern or text on the surface of the material.
5) Polylaminate material “C” type perforation line punching system
It is used to punch perforation lines for easy tearing on the polylaminate material capsule.
6) PVC material Skirt perforation line punching system
It is used to punch the dotted hole for tearing on the PVC material or cut on the edge for easy tearing.
7) Automatic gluing system
It is to apply the adhesive glue evenly to the edges of the skirt material as required.
8) Tear off tape gluing system
It is to accurately affix the material tape used for tear off capsule to the desired location.
9) Color mark tracking system
The system can track any printing color mark on the main material and can be accurately sent to the main material cutting knife and cut the material into fan-shaped pieces according to the length as setting.
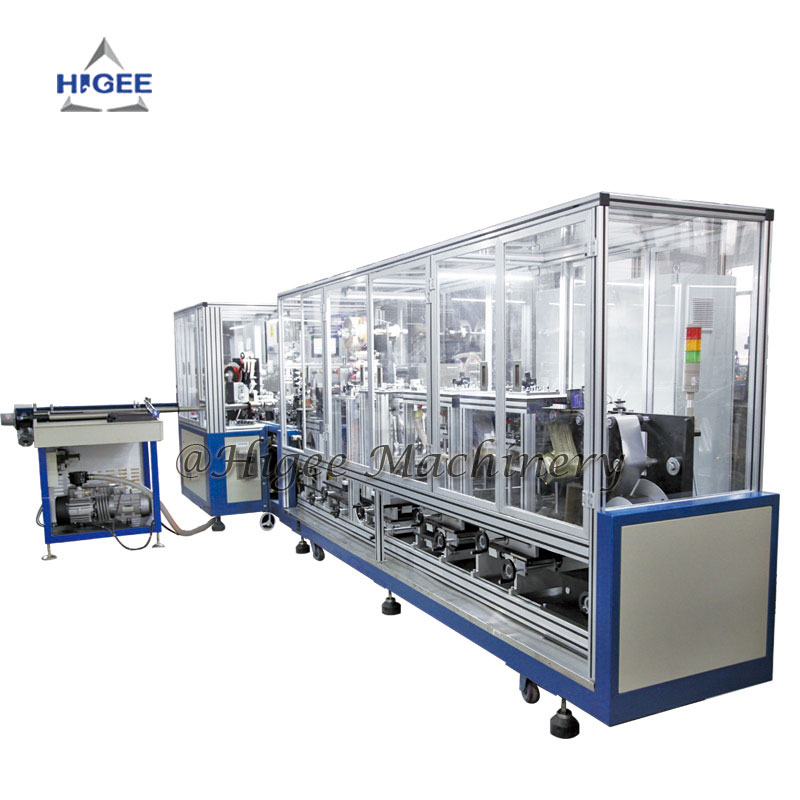
For PVC capsule making:
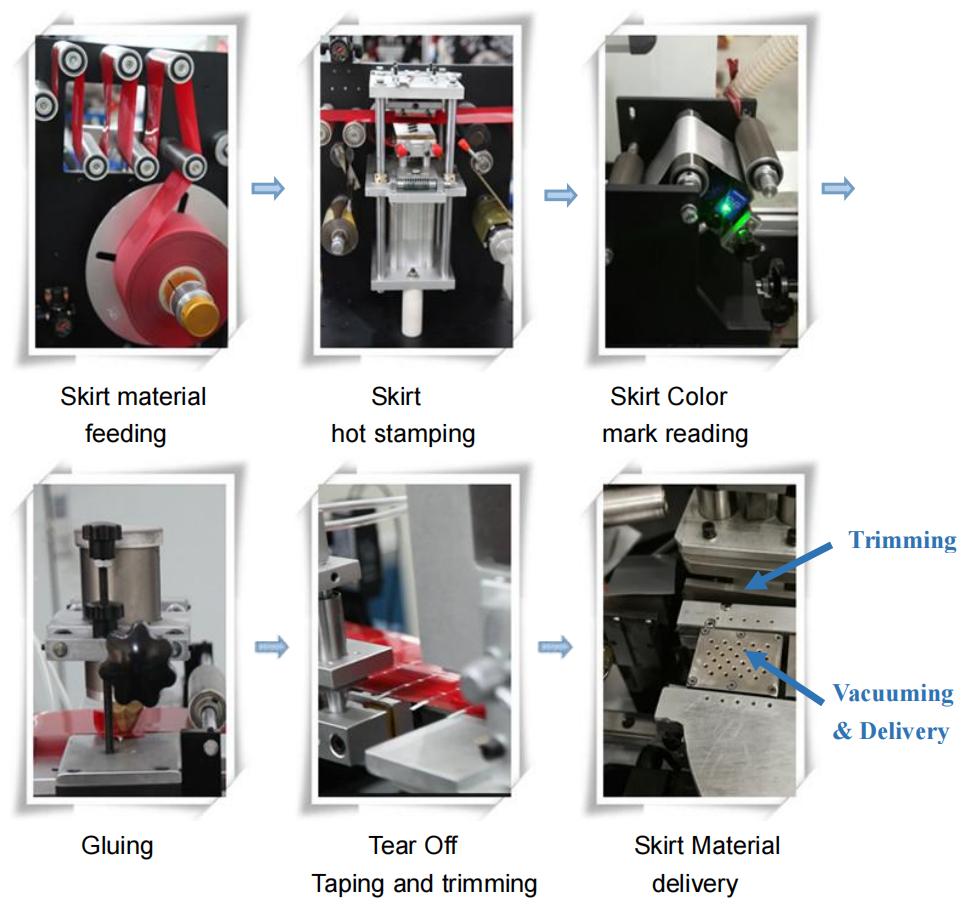
For Polylam capsule making:
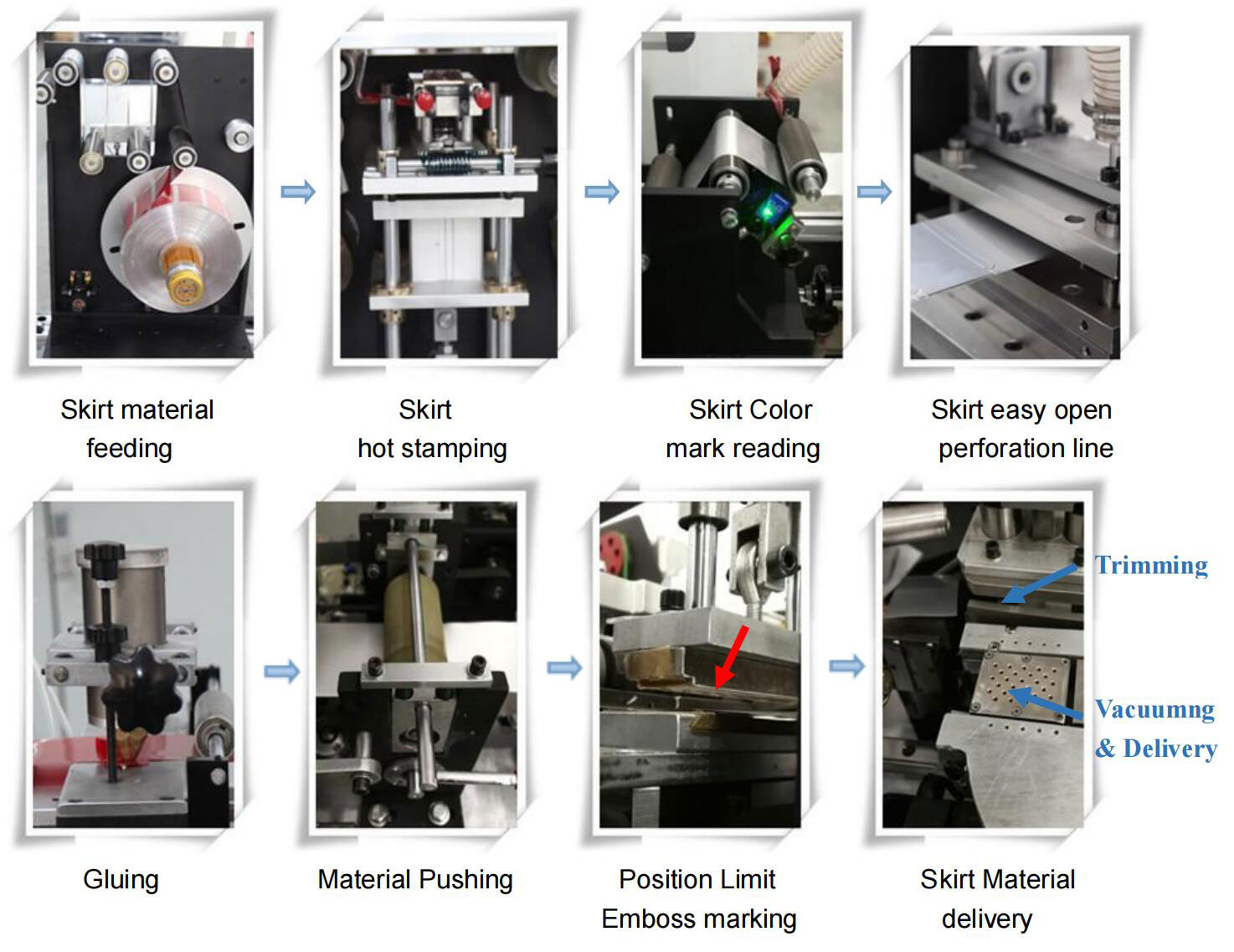
2. Main workstation
The center of the main workbench is equipped with a rotating mold turntable, with 12 capsule forming moulds, each is separated by 30°. There are 12 stations separated by 30° on the table. The function of each station is as follows:
<01> The mold on the station sucks one of the material sheets through the vacuum suction hole and transfers it to the <02> station. The winding device winds the sheet firmly to the mould by the adhesive previously coated on the other edge of the capsule material sheet. Transfer to the <03> station for the first time pressing at the joint, transfer to the <04> station for the top end curling of the polylaminate capsule material, and make a second pressing on the adhesive joint. Transfer to the <05> station, the PVC capsule can be formed by hot air heating shrinking, transfer to the <06> station to flatten the PVC capsule top end, and this station is also equipped with photoelectric missing capsule detection function (If no capsule is detected, the following related stations will stop). Transfer to the <07> station to install the top cover, and also equipped with a color mark detection, through which the color mark printed on the material can be accurately conveyed to the desired position of the top cover mould. Transfer to the <08> station for heat sealing of the top cover. Transfer to the <09> station for top embossing or hot stamping. Transfer to the <10> station which can do printing for the raised portion of the top pattern. Transfer to the <11> station to use compressed air to withdraw the finished capsule from the mold, and stack the capsule with the set quantity. Transfer to the <12> station when the capsule is not withdrawn. Turn off the machine and then pull out the capsule. Or the machine rotates to the next station, and the motor will stop feeding automatically (It is invalid if the detection function is turned off).
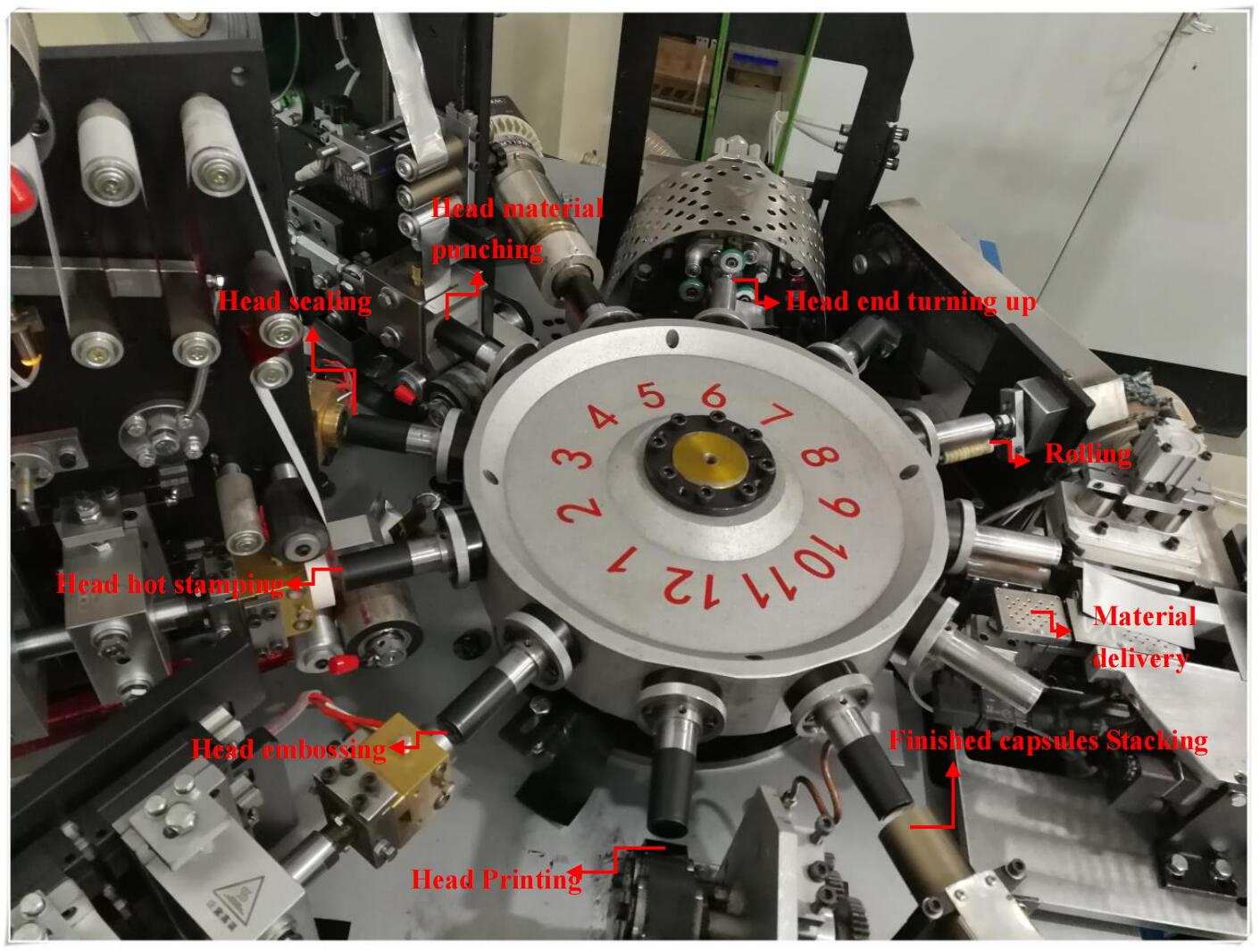
More pictures for reference:
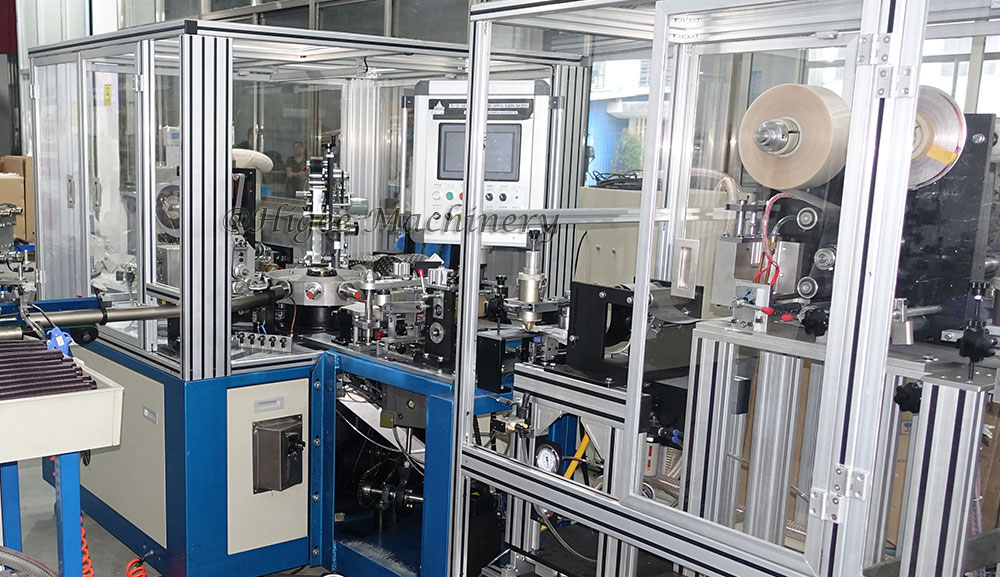
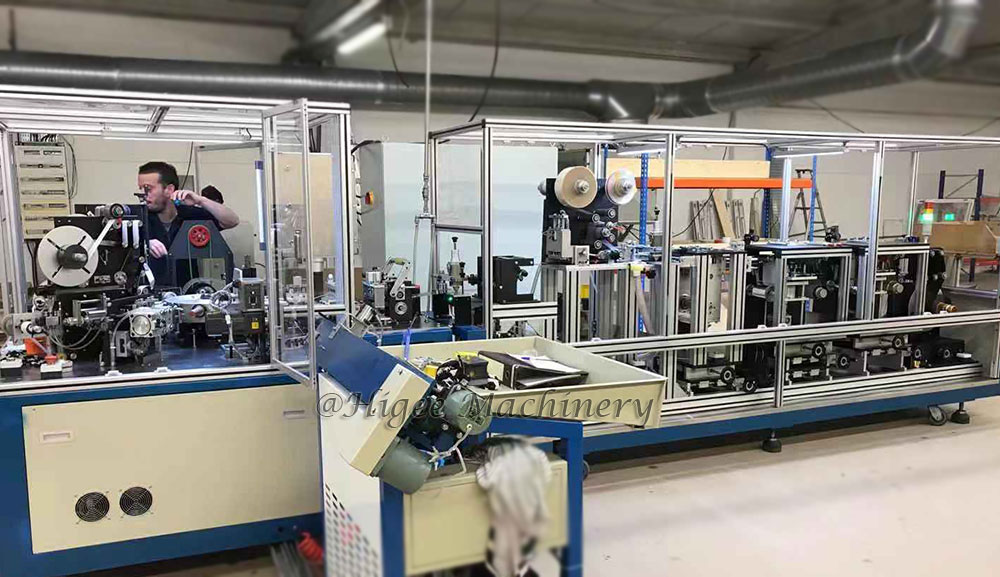
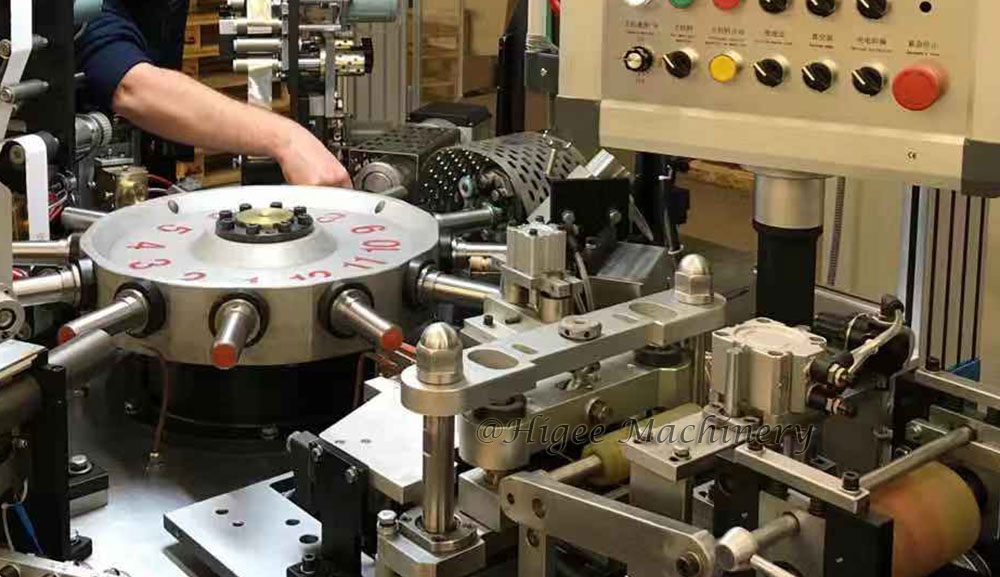
Option: with protection glass window
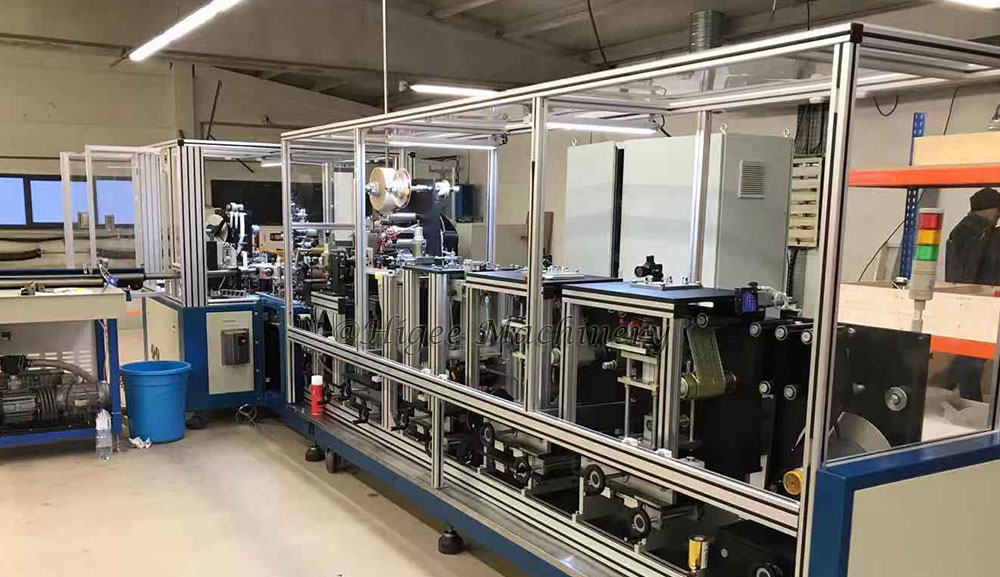
Wine Capsule Machine Workshop View:
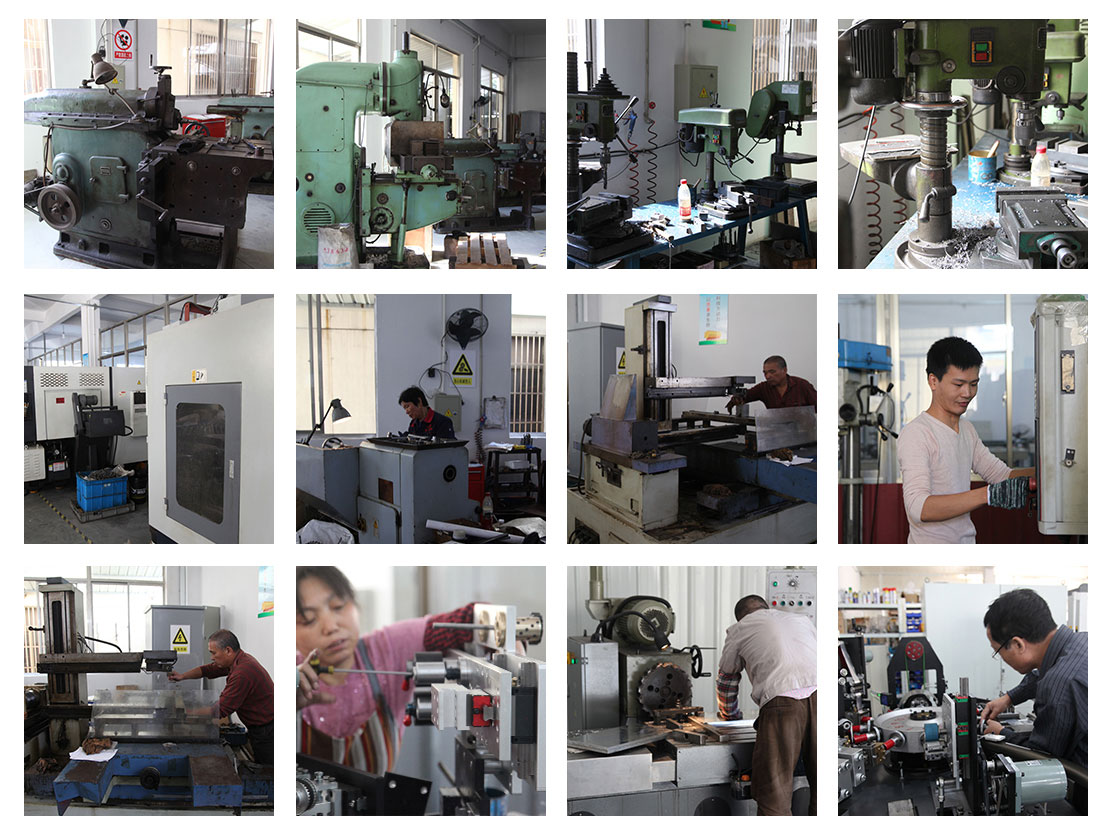